
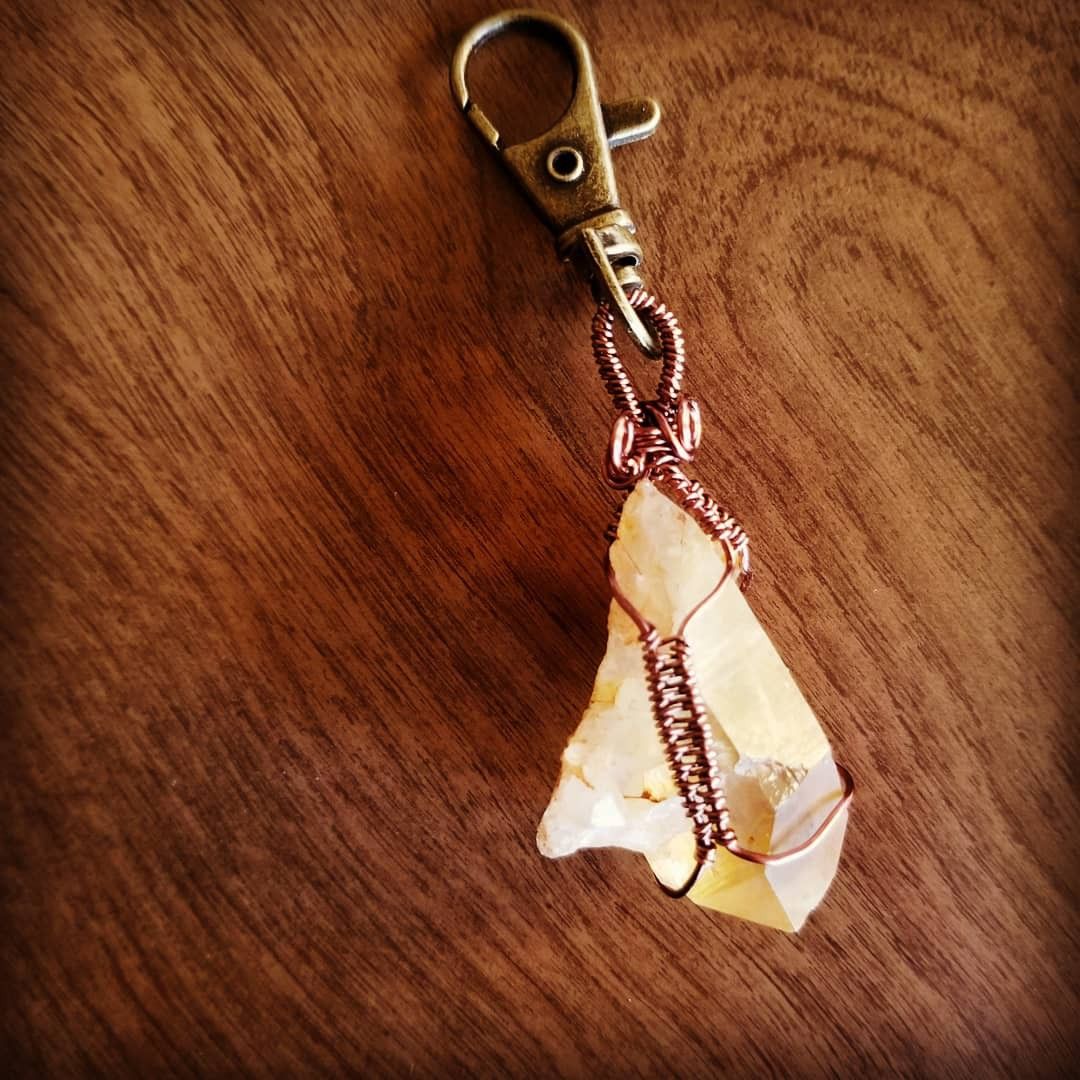
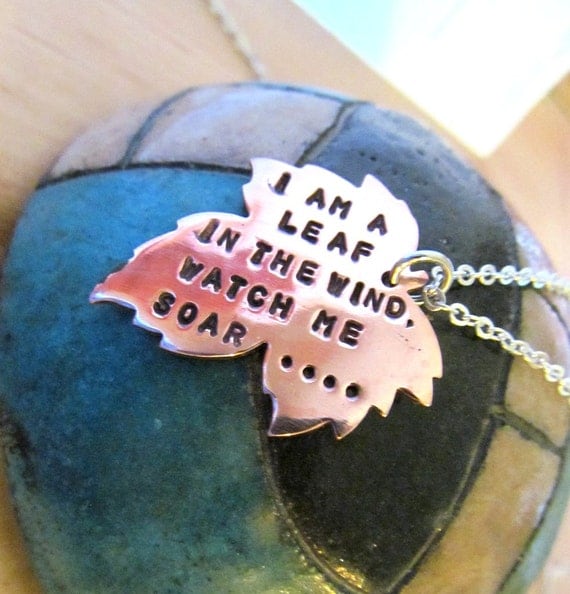
The use of such distributed buoyancy is mainly aimed at minimizing the overall cable dynamic responses and accommodating the cable dynamic tension or curvature changes in harsh weather conditions, by decoupling the platform motion from the cable touchdown point at the seabed. Secure fastening and precise positioning of buoyancy modules are ensured by using internal clamps. In any case, there is a requirement for a design of buoyancy modules (typically made of synthetic foams) to be distributed along a certain mid-water part of the cable. The W-type cable may be used for connecting between the two floating wind turbines or between the floating substation and wind turbines, whereas the lazy wave cable may be used as an interarray, interplatform and export cable. Dynamic power cable concepts: (a) interarray cable (b) export cable. In terms of the design, this requirement can be translated into a floating support structure minimum rotational stiffness ( Section 11.2.2).įigure 13.8.
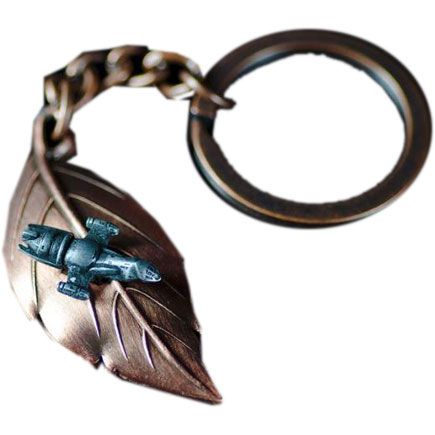
It is important to remember that this is the total angle of inclination, the sum of the static and the dynamic angles of oscillations, due, respectively, to the average value (mainly due to the wind) and the oscillation amplitude (mainly due to waves) of the inclining moments. The exact value of this maximum inclination angle is still open to discussion, but according to the literature a good starting value is 10 degree. Taking also into account the fact that many of the sub-systems of an offshore wind turbine (bearings, gearbox, generator, etc.) have been designed to operate close to the upright condition, it is necessary to impose a maximum roll/pitch inclination angle. As a consequence, there is very little experience in estimating the performance of wind turbines at large inclination angles, and relatively few data have been presented in literature. While FOWT systems can experience relatively large inclination angles (in roll and/or pitch), onshore and fixed-to-seabed offshore wind turbines do not experience such angles. Borg, in Offshore Wind Farms, 2016 11.2.1.2 Maximum inclination angle
